top of page
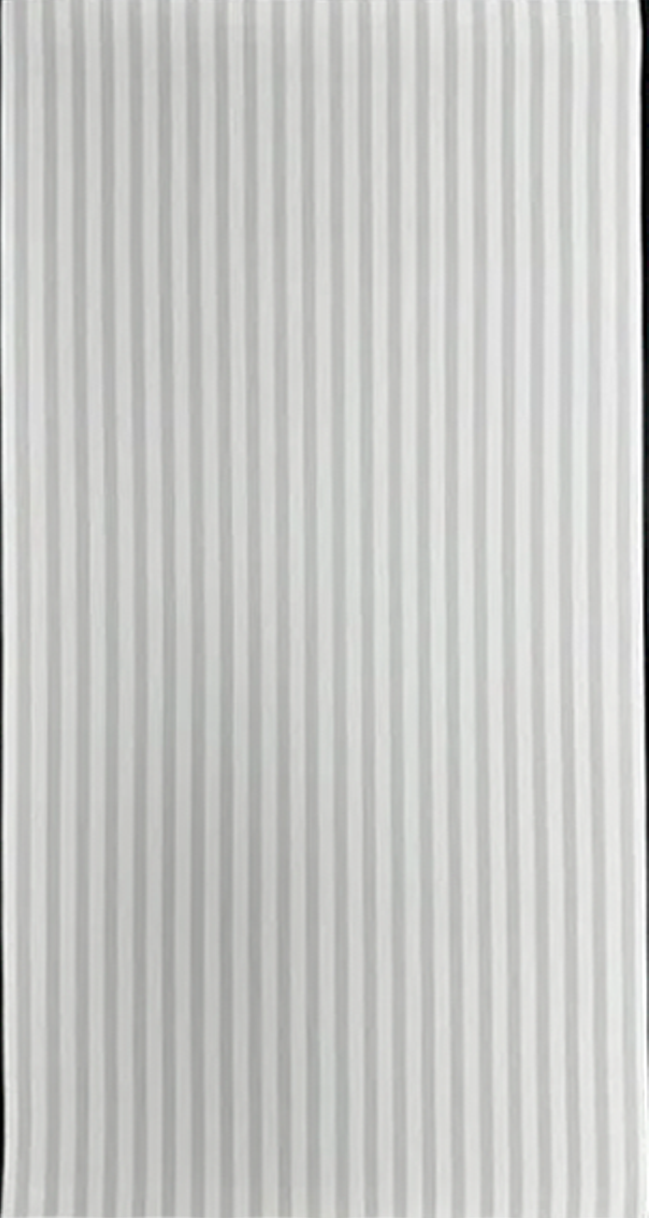

Frequently Asked Questions
The EV conversion industry is new and growing by leaps and bounds. Information that is pertinent today may not be so tomorrow. If you don't find answers to your specific questions here, please contact us.
-
Q- What are the benefits of using an electric vehicle gear reducer (TTI Brand: TorqueBox®)?A- Gear reduction multiplies the available torque of a motor an amount equal to the reduction ratio. Keep in mind the reduction also reduces driveshaft rpm by a factor of the gearbox ratio. Therefore a 2 to 1 reduction doubles the motors torque while a 3 to 1 triples the torque. Without a reduction gearbox (known as “direct drive”), you would need to use a much larger and more expensive motor to reach the same performance level of a smaller motor with a reduction gearbox. All OE electric vehicles on the road today are running a reduction gearbox of one design or another. All Tesla vehicles run gearboxes and while they are a single speed and do not shift they generally run a reduction ratio between 9 and 12 to 1 in their transaxle system. Running a TorqueBox® brand gearbox in a vehicle with a gear ratio in the drive axle(s), you simple multiply the TorqueBox® ratio by the ring and pinion ratio to find your final drive ratio (FDR). example In a vehicle with a 4.10 to 1 ring and pinion and a 1.90 TorqueBox® you have an FDR of 4.10 x 1.9 = 7.79 to 1, while our new 3.00 to 1 TorqueBox® would give an FDR of 12.30 to 1. To put this math into torque numbers, a motor with 300 lb ft of torque and the 7.79 FDR would be 2,337 lb ft of torque to the tires, while the same vehicle with our 3.00 to 1 TorqueBox® would realize an FDR of 3,690 lb ft of torque to the tires. Caution: Keep the rpm reduction in the equation! If your motor is rpm limited to 6000 rpm the tire rotation is reduced to 770 rpm with the 1.90 to 1 TorqueBox® while with the 3.00 to 1 TorqueBox®, it is reduced all the way down to 488 rpm and while this increases torque and acceleration, this will limit your vehicles top speed dramatically. That said the 1.90 to 1 ratio is best for the limited rpm motors and the 3.00 to 1 works well with the high rpm motors. Note: the numbers and explanations found here are general. Call us or your preferred installer to get the exact numbers and recommendations for your build. In summary; running a reduction box allows big motor performance from a smaller, more economical motor.
-
Q- What is the best gearbox for my application?A- A TorqueBox of course. The real question is what ratio TorqueBox® would best suit my vehicle and driving style. Really low budget and most all of the early gas to ev conversions just made an adapter and coupler to bolt the electric motor to the existing "gas appropriate" multiple speed manual transmission. Then they would typically run in either second or third gear. This is very energy inefficient. A proper reduction gearbox saves weight and reduces frictional losses which extends the operating range of the vehicle. A reverse gear is not needed as most electric motors can simply be run backwards for reverse.
-
Q- What reduction ratios are available in a TorqueBox®?A- We have marketed a 1.90 to 1 ratio-based reduction gearbox under the TorqueBox® name for over ten years. At SEMA 2023, we debuted a re-designed planetary reduction gearbox with a 3.00 to 1 ratio. With these two TorqueBox® ratios, we have an ideal ratio for 95% of the single ev conversion market. We also debuted a new non-planetary Dual Motor "Torque Vectoring Capable" TorqueBox® and initially offer this in three ratios: 3.80, 5.14, and 5.62 to 1 reduction ratios.
-
Q- Is the ev TorqueBox® a manual or automatic transmission?A- The ev TorqueBox® is based on a planetary gear system like found in automatic transmissions but is a single speed that does not shift. This box is more accurately referred to as a reduction gearbox or gear reducer. The planetary gear system requires Synthetic ATF fluid and can be damaged by running any other lubricant. Never run a motor oil or gear oil in a planetary-based TorqueBox® brand reduction gearbox.
-
Q- Can an ev TorqueBox® be customized or upgraded for better performance?A- While not every vehicle needs its TorqueBox® customized we do offer several upgrades for performance improvements when they are needed. For performance vehicles, we offer micro shot peened sun gears. The driven or reaction sun gear is splined to the input shaft and turns at motor speed while driving three pinion gears. The fixed sun gear does not move but is in constant mesh with three pinion gears. Think of each sun gear as being in a fight against three other gears at the same time. The wear rate is then potentially three times that of a single pinion gear and this is why we recommend shot peening of these two vital gears. In extreme performance or in HD commercial applications we recommend shot peening the entire gear set. Most all transmission gears are made from 8620 steel alloy, this is a great material that balances strength and longevity. When the vehicle is an extreme performance (over 500 HP) or HD commercial (over 10,000lbs) and strength outways longevity, then we recommend our Extreme Performance EN-36 material gear set with all gears getting the shot peen process.
-
Q- How can I be sure that a TorqueBox® will fit in the tunnel of my vehicle?A- The TorqueBox® was designed to fit in tight tunnels and compact spaces. A diameter of only eight (8) inches and length of 10-12 inches allows this unit to fit in tunnels of cars like '65 Mustangs, Mazda Miatas and MGs.
-
Q - Can the TorqueBox® handle electric motors with high torque and high rpm?A - A re-sounding yes! The 1.90 TorqueBox® can handle upwards of 12,000 rpm and 900 Nm of torque in it stock form and even more with a few optional upgrades. Our new 3.00 TorqueBox® can handle up to 20,000 rpm and is rated at up to 1200 hp and 1200 ft lbs of torque right out of the box and without any upgrades from stock.
-
Q- Are there any specific maintenance requirements for the ev TorqueBox®?A- Yes, the ev TorqueBox® runs on a very small amount of synthetic ATF and so should be changed annually or every 7000 miles, whichever comes first. TTI installs a max temperature sticker on every TorqueBox. The sticker records the highest temperature reached. All TorqueBoxes are dyno tested to 200 degrees F. The sticker registers to 230 F. If in operation a specific vehicle runs the sticker above 225 degrees F, even once, then we recommend an external pump and cooler be added to the system to offer longevity to the TorqueBox. Remember, the 100% synthetic ATF is the lifeblood of the TorqueBox, keep it under 225 degrees F and clean, and you can expect a long gearbox life and loads of fun.
-
Q- Can I use motor oil or gear oil in a TorqueBox®?A- Our planetary-based TorqueBox® units use directed splash lubrication and rely on oil misting to lubricate some of the most critical areas. Only a full synthetic ATF fluid has the unique misting qualities needed. However, our Dual Motor Torque Vectoring Capable TorqueBox® is not planetary-based and here were do recommend a full synthetic 75W90 gear oil.
-
Q- Can the TorqueBox® be used in marine applications?A- Yes, we have been used in numerous inboard and even a few outboard applications.
-
Q- What other components besides a motor, inverter, gearbox and battery pack will be needed to complete my conversion?"A- Not all conversions are the same, but here is a very basic list of items in addition to those listed above. VCU- Vehicle Control Unit, this is a master controller to manage all components in your EV. BMS - Battery Management System. Most Original Equipment packs incorporate all or at least most of the management within the pack itself. However, in most DIY projects, the BMS is a separate component. PDU - Power Distribution Unit, comes in both high and low voltage systems, high voltage units are commonly called a contactor box. Coolant pump(s) on liquid cooled systems. If only running a single pump get the coolest fluid to the temperature sensitive inverter first and to the more heat-tolerant motor last. Power Steering - If needed, must be addressed. Some later model vehicles already have electronic assist steering and you can easily communicate and manipulate what is already there. On older vehicles that need power steering, you may need to add a small electric motor dedicated to power a conventional hydraulic pump. In lighter vehicles, you may be able to just eliminate the power assist all together. We had power steering on our 1999 Miata and just eliminated it when converting to electric. AC Compressor - There are a number of small but very capable ac compressors on the market that can be tied into the ac system of the vehicle to keep the driving compartment cool. This can also be used to chill water for component or battery box cooling. Most ac compressors are of the high voltage variety and draw from the battery pack via the PDU or Contactor Box.. Cab/Battery heating - On our very first conversion, we ran all liquid cooled components and just a single coolant pump. We plumbed the hottest coolant coming from the motor directly to the existing heater core of the vehicle and quickly found this was a very inadequate source of cab heat. The electric drive train components just do not make enough heat to heat the average vehicle, especially in a cold climate. There are high voltage electric heaters available and, properly sized, they can work very well. However, they do reduce range if you need to use them very much. Another option, all though more expensive, is to design or better yet use a good heat pump system from a late model ev, like Tesla. DC to DC Converter - Needed to drop pack voltage down to approximately 13.5 volts to run all the 12v systems like wipers, interior and exterior lights heater fan and your stereo of the car. These come in various capacities and either liquid or air cooled with fans. A 1kW unit will more than suffice for the basic conversion if not running extra electronic equipment. Liquid cooled is nice but for the more basic conversions air cooled systems can work. On Board Battery Charger - They come in different capacities and in either air or liquid cooled. Most DIY conversions will have 6.6kW or lower. Actually 3.3 kW is popular. There are many options available, even combo units with charger and DC to DC combined. Most DIY conversions use level one (household 115v current) or level two charging (can be 115v or 230v but higher amperage than a level one). Then there is DC fast charging which is only found in a few of the high dollar conversions and many, but not all, OE electric vehicles. Dealing with high voltage charging is expensive and must be handled with a safety-first approach. Battery pack cooling becomes very necessary when using DC fast charging. There are many smaller items like gauges, throttles, shift module with buttons and lights, mounting for motor, gearbox and all other components. BTW- it is important to isolate all electronic components from road vibrations. This also leads to quieter vehicle operation. Then there is all the needed hardware and wiring including the dual insulated high voltage (hv) ev cables. Welding cable use is a thing of the past. You want to use a safety approved hv cable and can expect to spend $10 to $13 a foot depending on diameter. Low voltage systems can run smaller cables but high voltage systems usually run 2/0 cable and some as much as 4/0 cable. Always try to find double insulated cables in either red or orange color and always keep the cable lengths as short as practical.
-
Q- What is the best battery chemistry and pack size to run for my application?A- Now here is a subject that was easier to answer a couple years ago than it is today and yes there are many variables here as well. We will try to keep the answer informative and concise. To start with there are three basic physical battery types used in conversions: Prismatic cells (built like a brick with ridged exterior dimensions); Pouch cells (soft and flexible like the name implies); and, Tesla popular cylindrical cell, similar to an AA battery, only larger. All three physical types are available with several popular chemistries. Most, but not all, Prismatic cells are described as a Lithium Iron Phosphate chemistry. They are considered the safest chemistry. Typically, Prismatic cells have a 3.2v nominal voltage and are what we call "a little sleepy", meaning they don't accept or release electrons quickly. This is an OK battery for most DIY builds and less than high performance vehicles. Other popular chemistries are Lithium Polymer, Lithium Nickle Manganese Cobalt Oxide, Sodium, Nickle Silicon Aluminum and Sulfur. Some of these performance cells offer 3.7v or slightly higher nominal voltage. All of these have a lithium solution and the other words found in the cells name generally describe the material or coatings used in construction of the cell and primarily the anode and cathode (positive and negative polls) within the cell. Billions of dollars have been spent on battery improvements over just the last few years and even more will be spent over the next few years to maximize the energy density, longevity and charge cycle capability. The next great gain in battery cell technology will likely be the solid-state battery offering many advantages over today's liquid lithium solution cells. Which is best for you is a complex subject. Many of the converters today are using used Tesla modules from salvaged vehicles. A typical Tesla module holds 444 individual cylindrical cells and can be used in both series and parallel configurations or combinations thereof to create the max voltage and amperage desired. Tesla uses 6000 to 7000 cells or around 16 of these modules in a single car. Last I looked the aftermarket was asking between $1200 and $1400 per module. Because these modules are becoming increasingly popular the prices are continually climbing. There are of course many other options available. Most lithium-based batteries are made in either China, Japan or Korea and most have distributors in the US and Europe. If you are doing your own conversion and building your own packs then hit the Internet hard, see what others are currently doing and find your best deal. Ideally though, you will want to deal with a company who has experience designing and building battery packs. Safety and battery life come through proper battery management, so unless you have done this successfully, lean on others with a good reputation.
-
Q- I see you offer an optional ParkLock system for your gearbox, do I need it and if so, why?"A- Our ParkLock is a system for locking the gearbox, and thus the driveline, to prevent the vehicle from rolling away when parked. According to DOT for a vehicle to be road legal it must have a positive locking system to prevent rollaway other than the e-brake of the vehicle. The DOT goes on to say the locking mechanism must be applied as one in the same function as placing the vehicle in the park position, it should not be a separate function. Setting an e-brake when parking even with a transmission lock is accepted and recommended by most car manufacturers. The ev world is rapidly changing but at the time of our ParkLock system development and at the time of this writing, the ParkLock system is a sound investment in safety. We have all heard horror stories about cars and especially ev conversions rolling away. I know of one that ended up in a neighbors swimming pool at the bottom of the hill. ParkLock would have prevented this.
-
Q- Why do you not offer a yoke automatically with every gearbox?A- TTI makes ev gearboxes with 27 spline shafts, same as GM PG and Turbo 350 transmissions so many conversions can use their existing yoke, once modified. The modification consists of shorting the barrel and in some cases undercutting the internal spline. For most people it is best to order a new cast or billet yoke along with your TorqueBox purchase. This way the modifications are handled by a company that has been doing this for over eleven years. I suggest you watch our Driveline Video Series and especially the one on selecting a yoke for your build. We also make a bolt-on (fixed) yoke with 32 splines similar to a GM Th400 output spline. In this case, the yoke is modified with our sealing system so the yoke usually needs to be supplied by us. Call (623 755 8214) or email (info@torquetrends.com) our tech department with any yoke questions.
-
Q- Can I use my existing a-yoke on a planetary-based TorqueBox®?A- No, the TorqueBox® was designed to be as compact as possible without giving up strength. For this reason the yoke (whether fixed of slip) must be modified by Torque Trends.
Bottom of Page
bottom of page